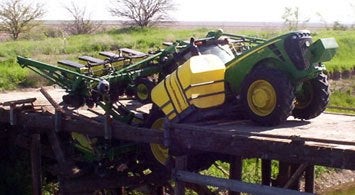
While walking the 1.2 million square feet of the National Farm Machinery Show (NFMS) in Louisville with longtime mytractorforum.com member Mickey Latour, a Kentucky Department of Agriculture (KDA) booth demonstrating two common tractor related dangers caught our eye and became the seed for this article on tractor safety.
The first demonstration was conducted by Kimberly Field of KDA and covered power take off (PTO) safety. On hand was an electric power source coupled to a Bush Hog SQ148 rotary cutter via a PTO shaft. Field stressed the need for properly installed PTO shaft covers to be in place, then using a dummy, tucked a piece of loose fitting clothing into a exposed PTO coupling. What took place when the motor started graphically portrayed how dangerous an exposed PTO shaft could be. The good news is that PTO shaft covers are inexpensive, easy to install, and once installed never need to be removed (unless they are somehow damaged) even to do simple maintenance such as greasing the universal joints.
The second NFMS demonstration was conducted by Whitney Turner, also of KDA, covering how a tractor rollover protection system (ROPS) works. For this exhibition a John Deere 4105 was rotated on front and rear pivot points, first with the ROPS folded and then with it extended. Again the dummy strapped in the operator seat clearly fared poorly unless the ROPS was extended as designed.
Rollover protection isn’t just for conditions where a side over roll might be encountered. Too many injuries and deaths have occurred by tractors tipping backwards and crushing the operator. Usually this is caused by improper attachment of a chain above the axle centerline, but changing conditions, hills and slopes, and front and rear loads can all create dangerous conditions. And while you might hear tales of those convinced they were saved because their tractor did not have a ROPS during some encounter or that it was lowered, statistics prove the addition of ROPS to tractors and their use in conjunction with seatbelts saves lives.
With those two demonstrations firmly ingrained, we began to jot down other areas an operator needs to take into consideration. Seven came to mind.
Safety Switches
Over the years, manufacturers have added many safety features, some prompted by litigation, but also by a general desire to make tractor operation safer. In that context it makes no sense to override those safeties, yet barely a month goes by without a post on the forums asking how to disable those systems. Even our least favorite system – those preventing reverse operation while a PTO is engaged unless a button is pushed – are easy to get used to and over time become second nature.
Ballasting
We ran a feature covering tractor ballasting back in November, and though our focus then was on controlling wheel slip to improve efficiency, proper ballasting can also influence safety. Evenly distributing weight over the tractor wheels will yield maximum traction and stability. For example, a tractor equipped with a front-end loader (FEL) and carrying a full load with none or improper rear ballast will fight for traction. Conversely, too much of a load at the three-point hitch (3PH) will result in lessened front wheel traction and decreased steering control.
Tire Choice
Get a group of tractor operators together and bring up the subject of tire choice and there’s a good chance it will end with the parties involved agreeing to disagree. One area to agree on is that the reason to select a given type of tire is to get the maximum traction with the least ground damage under the conditions the tractor is most likely operated under. And traction is definitely a factor to consider for safe operation.
R1 (Ag) tires are generally considered the most aggressive and offer the highest degree of traction in sloppy conditions. They also can do a number on turf, especially lawns. R3 (Turf) tires offer the least damage, but are nearly useless in muddy conditions. R4 (Industrial) tires are a compromise, but like Ag tires, are considered by some to offer less side hill traction. Even with the correct tire choice, tire inflation is an area to pay careful attention to. Wheel spacers can also help get a wider, more stable stance.
Matching of Implements
Tractors may provide the power and traction to get the job done, but the implement is what does the lifting, cutting, raking or harvesting. And most will want to get the most done of these tasks in the shortest period of time. As long as the horsepower requirement the implement falls within the tractor output capability you should be good to go, right? Not necessarily. The size and weight of the implement play a big part in the compatibility. In the case of a rotary cutter, paying attention to the whole picture might just lead you to choose a 5’ implement over a 6’, and in the process hanging less weight on the 3PH and not as far out behind. This will improve both stability and control.
Loader and Implement Use
A FEL is one of the most handy and productive implements invented for use with a tractor. Even in a light-duty machine such as a subcompact (SCUT) where lift capacities might be 400-600 lbs, a loader goes light years towards making that wheelbarrow obsolete. In large, heavy-duty larger tractor instances, lift capacities might be several tons or more. And though that FEL might be rated to have that max lift capacity at some outrageous lift height, operating the tractor at that height increases the danger of tipping. The same can be said for any 3PH implement. Experienced operators keep loaders and implements as close to the ground as possible. This improves both the center of gravity and tipping safety.
Equipment Maintenance
It goes without saying that maintaining your equipment properly results in longer life, lessened repair costs, and less downtime. But maintenance is also an area that can influence overall safety. Experienced operators routinely inspect their equipment, looking for loose and/or missing guards, worn and/or damaged rotating parts, and increased noise and/or vibration. Heading off that problem before it becomes a big one is the proper attitude.
Situational Awareness and Conditions
While operating a tractor with manufacturer safety switches in place, ballasting to owner’s manual specifications, correct tire selection, implement matched to tractor and operated as low to the ground as possible, and everything properly maintained with all guards in place will make for safer operation, awareness of the situation and conditions is what brings it all together.
Experienced operators assess the situation and conditions, look for others in the area (people, pets/animals and other machinery), consider turf and soil condition, weather, obstacles that might have been introduced since the last pass over a field, and even their own physical condition. With a little rest and a fresh look, many accidents can be prevented. Lastly, if you’re not sure if a slope exceeds the safe capabilities of your tractor, an inclinometer can be useful in quantifying the degree. Just remember, conditions change and a safe degree one day may not be the next.
Safe operation of a tractor isn’t rocket science, but just a careful, deliberate thought process. Take steps today to make your creed “shiny side up; no one hurt.”