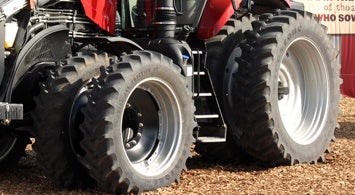
For maximum tractor performance in the field there are many variables to consider. Starting with the tractor horsepower and drawbar – or three point hitch (3PH) – capacity, the implement used and size along with required ballast and tire selection are important influencing factors that must be taken into consideration. Tractor.com covered ballasting in Nov. of 2013 and tire choice in May of 2014, but in our travels we’ve observed enough examples of improper tire inflation to pen this article.
Maximum field performance not only means efficient tilling, planting, baling and harvesting, but also minimized ground compaction, increased tractor driveline life, better fuel usage, and increased profitability. With so many positive attributes associated with proper tire inflation, it’s easy to wonder why such a simple variable is so misunderstood and/or ignored. Simply put, what water is to a radiator, oil is to an engine, air is to a tire. If you don’t have water, oil or air in the proper amount, failure can occur.
Tractive efficiency is a measure of how well a tractor uses available power to pull an implement through the soil. Tractive performance is a balance of field performance, maximization of tire wear, elimination of power hop, and minimization of soil compaction. Radial tires are documented to have a big advantage over their bias-ply counterparts. Radial tires, though, require a more careful tire pressure management program. For the purpose of this article, we will focus on radial tires.
Ask almost any farmer what tire pressure is correct and you’ll get a wide range of answers. Some might say 15 psi is correct, that three or four lugs should be on the ground, or low in the paddock, high on the road. Many of those answers may be based on experience that has worked. But with tests showing incorrect tire pressure can waste as much as 20-40% engine power through slip and increased rolling resistance (meaning a 210 hp tractor might only be putting 115 hp to the ground) the only way to ensure maximum performance is to check pressure against manufacture recommendations for load and speed.
To determine the correct tire pressure you must first determine what the load and tractor weight for each axle is. To do so, begin by weighing the tractor on a grain or truck scale, then weigh each axle with the desired implement on it to get the weight per axle. If a 3PH implement is to be used, weigh the front axle with the implement down and then weigh the rear axle with the implement raised. Next determine if the ballasting is correct. General ballast recommendations are: 2WD 25% front/75% rear, MFWH 35% front/65% rear, and 4WD 55% front/ 45% rear. Once ballasting is correct, the tire can pressure can be checked and set.
Correct tire pressure for the load and speed will be manufacturer specific with each publishing charts with their recommendations. For example, Firestone publishes this multi-page PDF, while Goodyear (Titan) uses an online form.
To check tire pressure, use a calibrated pressure gauge. We recommend a system of two gauges be used to ensure a damaged gauge is picked up on before a tractor with an improperly inflated tire is sent into the field. Check should be done daily and early in the morning. While checking tire pressure, it is a good time to inspect the tires for wear, tread depth, and abnormalities such as cracking or sidewall fatigue. And if you aren’t already, begin a system of recording tire pressure readings for tracking and to aid in future productivity (and tire) decisions. Lastly, don’t underestimate the importance of a dust valve cover. All tire valves leak to some degree and the dust cap with rubber seal can help prevent air loss.
A modern improvement slowly migrating from over-the-road semi-tractor use is Central Tire Inflation (CTI) systems. Though often expensive ($7-20K installed), over the life of high horsepower tractor, a payback can be realized. Less expensive alternatives such as the Tyredog monitoring system can be had for $150 to $500 depending on model chosen. Not sure of the payback? Remember, operating at just 10% under pressure and tire life can be reduced by 15% or more. Conversely, operating at 20% over inflation and performance can suffer as much as 30%. Since 10% or 20% can be a very low PSI change, it’s wise to start checking those tires daily and begin reaping the many easily claimed benefits.
Dos and Don’ts
Do: Check air pressure often. Daily is best, but at least weekly.
Do: Use a calibrated pressure gauge. A system of two is highly recommended.
Do: Visually inspect the tires for wear and abnormalities.
Do: Check pressure in the morning when cold. Remember, manufacturer tire pressure recommendations are all cold temperature.
Do: Know your tractor weight per axle and be sure ballasting is at recommended levels.
Don’t: Overinflate. Over inflation increases ground compaction and decreases tractive efficiency. Ride quality also decreases.
Don’t: Underinflate. Under inflation can damage the tire construction and reduce life.
Don’t: Procrastinate. Start paying attention to tire pressures today.